Strategy and businesses
Cochlear Implants business
Sonovaʼs Cochlear Implants business operates under the Advanced Bionics brand, a recognized technology leader that employs approximately 900 people and is active in 85 countries worldwide.
A cochlear implant is a unique solution for a major or complete loss of hearing. Unlike a hearing aid, which amplifies sound, a cochlear implant electrically stimulates the hearing nerve directly. A sound processor worn behind the ear converts sound into the electrical signal transmitted to the implant. Every part of this system offers opportunities for technological advances that can create significant improvement in the quality of life for recipients and help them on their journey towards hearing self-sufficiency.
Benefiting from Marvelʼs advantages
Advanced Bionics gains a unique competitive advantage from its long-standing R&D collaboration with Phonak, Sonovaʼs premium hearing instrument brand. This allows advances in Phonak sound quality, connectivity, programming, and user control to be made available through Advanced Bionics sound processors. In this context, we are delighted this year to have received regulatory approval for our new Naída™ CI Marvel and Sky CI™ Marvel processors, which bring the breakthrough features of Phonakʼs Marvel platform – automatic adjustment to different listening environments with AutoSense™ OS 3.0, universal Bluetooth® connectivity, hands-free phone calling, integrated RogerDirect™ wireless communication – to adult and child recipients worldwide.
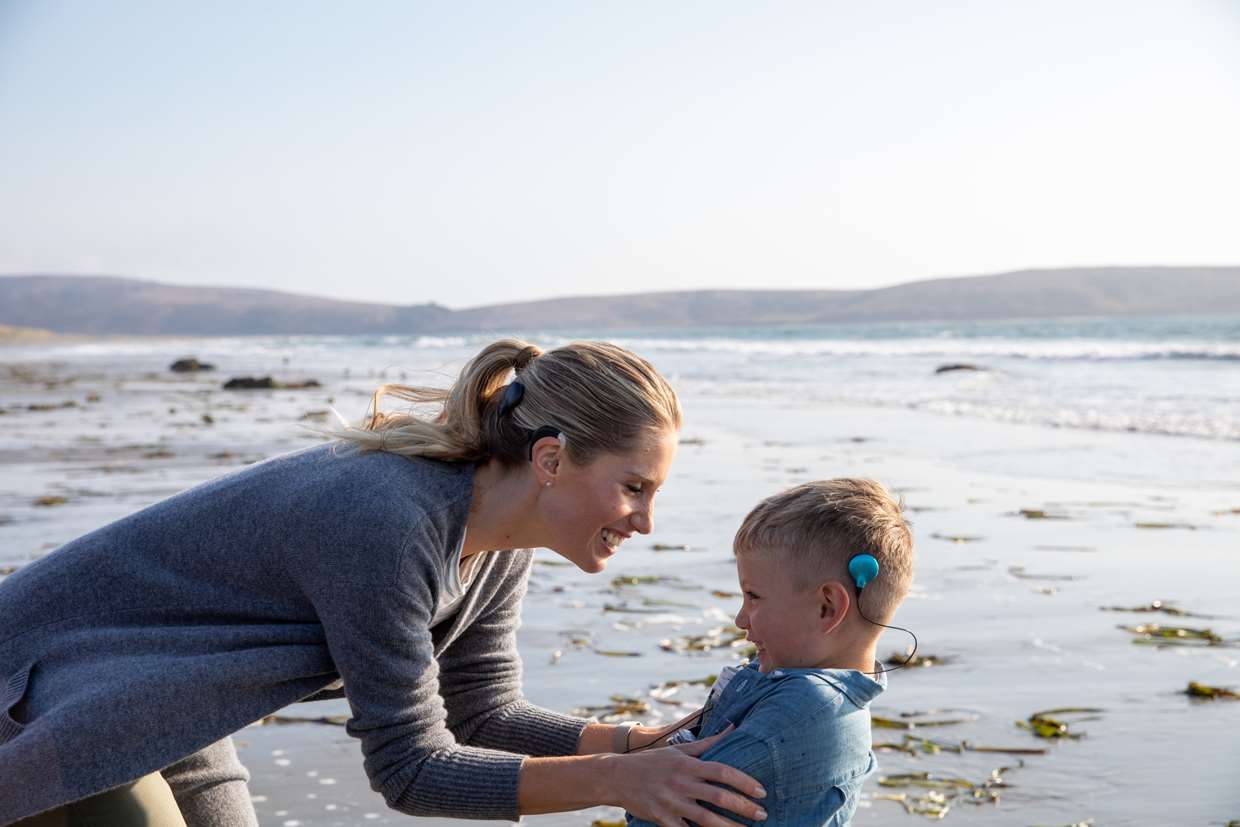
We have also introduced new fitting software, Target CI, which replicates for our sound processors the functionality, look and feel of Phonakʼs hearing aid fitting. This is advantageous for the majority of audiologists who work in both areas, particularly when fitting “bimodal” recipients who have a sound processor on one ear and a hearing aid on the other. Target CI is the first fitting software that allows these patients to have fitting for both ears done by the same software in the same session.
To bring these advances to the market meant developing a portfolio of 48 separate products – hardware, software, accessories – integrated into a single system. Strong collaboration across Sonova is the key that makes this possible.
Focus on quality
In February 2020, Advanced Bionics announced a voluntary field corrective action, retrieving the unimplanted initial version our HiRes™ Ultra and Ultra 3D implants from the market because of an increase of reports of reduced hearing performance. We want to acknowledge the impact that this had on recipients and audiologists and surgeons who work with them.
We have taken a number of steps to support our recipients and customers and to further ensure the reliability of our products: we have increased monitoring and partnering with clinics, developing custom software tools and integrity testing to support their experience. We are actively communicating through our sales force to provide regular updates. We have made further improvements in product development and statistical testing, developing new reliability tests and studies and even more stringent requirements. In the revised version of these implants (launched in February 2020), we have not seen a single confirmed reoccurrence of the failure mode that prompted the retrieval of the initial version. Moreover, we are grateful that 95% of our top clinics who purchased from us before the voluntary field action have returned with new orders, and we are working hard to regain the remaining 5%.
Operational improvements for the long term
The COVID-19 pandemic had the greatest impact on Advanced Bionics among Sonovaʼs businesses, both because of the general postponement of elective surgeries and the local effects of the pandemic on our manufacturing facility in California. Our strategic position was that every response to the crisis should have lasting value to the business, so we accelerated our efforts to raise efficiency and lower costs, while improving reliability and assuring compliance with the new European medical device regulatory regime. We streamlined our supply chain and administrative functions, consolidating our US back-office with the Hearing Instruments business, and transferring financial functions in the EU to Sonovaʼs shared service center. In manufacturing, an intensive program of Kaizen workshops generated a 5% year-on-year improvement in productivity along with significant increases in product yield, materials use, and training efficiency. At the same time, we implemented processes to further ensure product reliability and quality control.